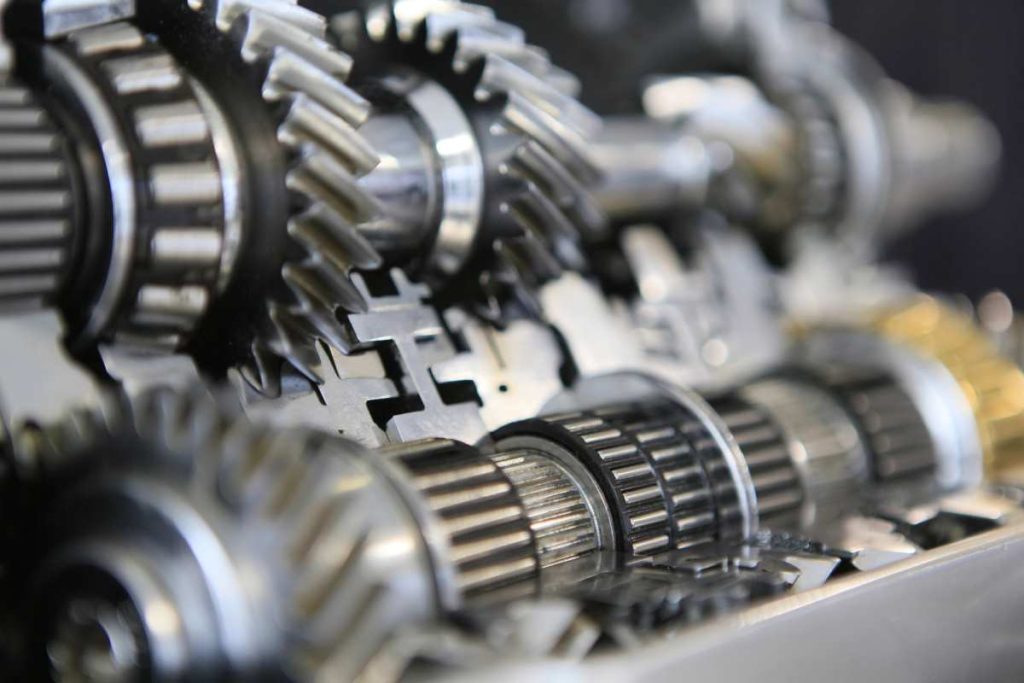
Un avance científico reciente ha permitido crear un recubrimiento a partir de residuos de plantas de mandioca que prácticamente elimina la fricción en piezas metálicas. Este descubrimiento tiene el potencial de mejorar la economía de combustible, prolongar la vida útil de las piezas móviles y generar enormes ahorros en una variedad de industrias.
El problema de la fricción
Las piezas móviles dentro de la maquinaria presentan un problema inherente: la fricción. Según un artículo de investigación reciente realizado por científicos de diversas instituciones en África y Estados Unidos, la fricción consume aproximadamente una quinta parte de toda la energía generada a nivel mundial cada año. Además, los daños causados por la fricción en la maquinaria representan entre el uno y el cuatro por ciento del PIB de las economías industrializadas. En la industria automotriz, aproximadamente el 30% del combustible utilizado en los vehículos de pasajeros se destina a superar la fricción.
Impacto en los costes y el ahorro de combustible
Reducir la fricción podría tener un impacto significativo en el costo de operar con máquinas y potencialmente ahorrar combustible en la operación de automóviles. El equipo de investigación, liderado por el presidente del Instituto Politécnico SUNY de Nueva York, Winston «Wole» Soboyejo, y el investigador postdoctoral Tabiri Kwayie Asumadu, decidió abordar el desafío de la fricción enfocándose en un concepto conocido como «superlubricidad». La superlubricidad es una condición de fricción casi nula entre dos materiales secos en movimiento en contacto entre sí.
Investigación
Hasta ahora, el comportamiento superlubricante solo se había observado entre partículas extremadamente pequeñas a escala nanométrica. Sin embargo, el nuevo estudio demuestra que el fenómeno es posible a escala macroscópica.
Para lograrlo, los investigadores depositaron carbono derivado de plantas de mandioca en superficies metálicas utilizando un proceso de tratamiento de biodesperdicio a alta temperatura y bajo costo. Una vez que el carbono se unió al metal, adquirió la estructura del grafeno, un material que consiste en una sola capa de átomos de carbono. Este material llenó las ranuras causadas por el desgaste, creando puntos de contacto exclusivamente de grafeno que protegieron el metal subyacente.
Resultados y aplicaciones
En las pruebas, el carbono unido a sustratos de acero y níquel resultó en un estado prácticamente sin fricción que se mantuvo robusto en condiciones normales durante aproximadamente 150,000 ciclos.
«Esta investigación realmente podría impactar en la mayoría de las industrias,» dijo Asumadu. «Desde el sector biomédico hasta el energético y prácticamente todo tipo de manufactura, este enfoque podría ayudar a prolongar la vida de las piezas de máquinas, reducir los costos de mantenimiento y reemplazo, y crear un futuro industrial más sostenible.»
Publicación de los hallazgos
El artículo que describe los hallazgos ha sido publicado en la revista Applied Materials Today.
Este avance no solo representa una innovación en el campo de los materiales y la ingeniería, sino que también ofrece una solución sostenible para reducir la dependencia de recursos y mejorar la eficiencia energética en diversas aplicaciones industriales.
Vía sunypoly.edu
Deja una respuesta