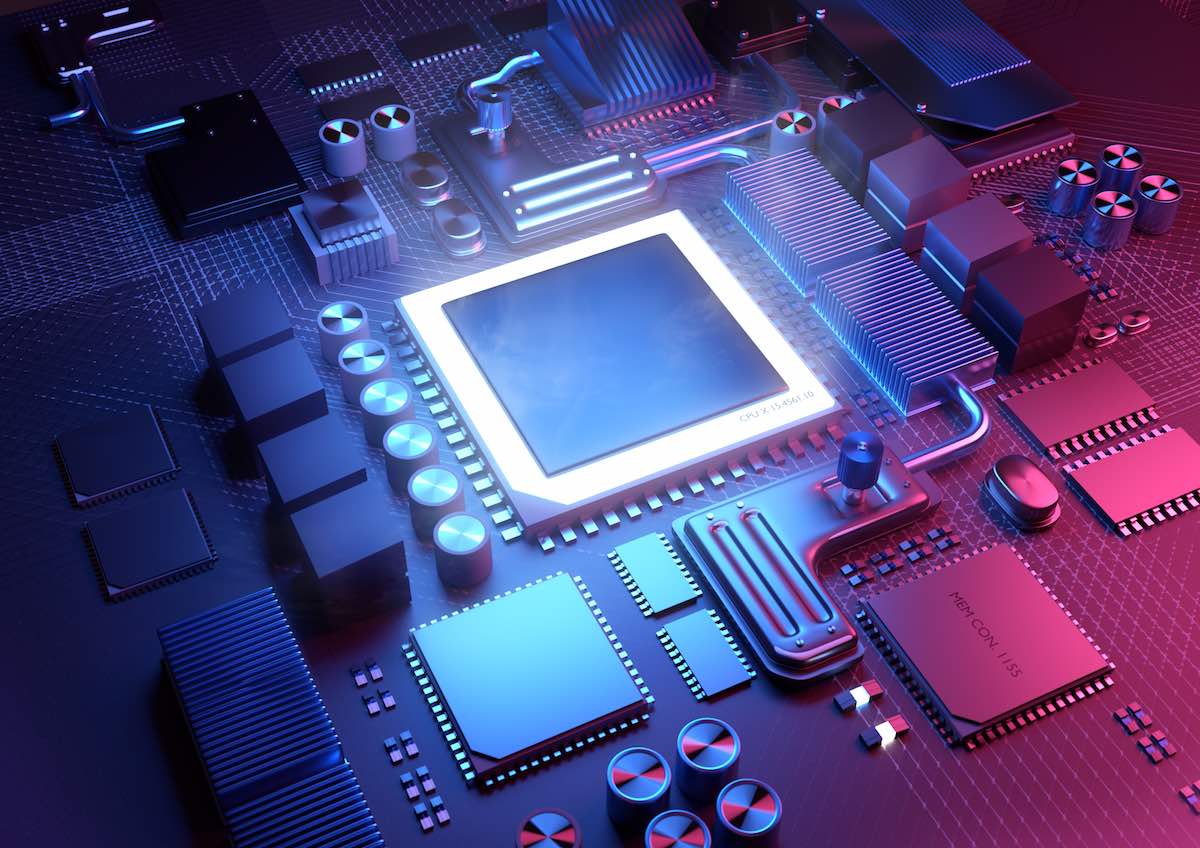
Una nueva tecnología de gestión térmica para dispositivos electrónicos reduce el volumen y mejora la refrigeración.
Los dispositivos electrónicos generan calor, y ese calor debe disiparse. Si no se disipa, las altas temperaturas pueden comprometer el funcionamiento de los dispositivos o incluso dañarlos y su entorno.
Ahora, un equipo de la UIUC y de la Universidad de Berkeley han desarrollado un nuevo método de refrigeración que ofrece una serie de ventajas, entre las que destaca la eficiencia del espacio que ofrece un aumento sustancial de la potencia por unidad de volumen de los dispositivos con respecto a los enfoques convencionales.
En primer lugar, pueden ser caras y difíciles de ampliar. Por ejemplo, a veces se utilizan disipadores de calor de diamante a nivel de chip, pero no son baratos.
Tarek Gebrael, autor principal y estudiante de doctorado en ingeniería mecánica de la UIUC
En segundo lugar, los métodos convencionales de difusión del calor suelen requerir que el difusor de calor y un disipador de calor, un dispositivo para disipar el calor de forma eficaz hacia el que el difusor dirige el calor, se coloquen en la parte superior del dispositivo electrónico.
Por desgracia, en muchos casos, la mayor parte del calor se genera debajo del dispositivo electrónico, lo que significa que el mecanismo de refrigeración no está donde debe estar para un rendimiento óptimo.
Tarek Gebrael
En tercer lugar, los disipadores de calor de última generación no pueden instalarse directamente en la superficie del dispositivo electrónico.
Hay que intercalar una capa de material de interfaz térmica para garantizar un buen contacto. Sin embargo, debido a sus pobres características de transferencia de calor, esa capa intermedia también introduce un impacto negativo en el rendimiento térmico.
Tarek Gebrael
La nueva solución resuelve estos tres problemas.
En primer lugar, el material principal utilizado es el cobre, que es relativamente barato.
En segundo lugar, el revestimiento de cobre «envuelve» completamente el dispositivo, cubriendo la parte superior, la inferior y los lados… un revestimiento conformado que cubre todas las superficies expuestas, de modo que no se descuida ninguna región productora de calor.
En tercer lugar, no es necesario un material de interfaz térmica; el dispositivo y el disipador de calor de cobre son esencialmente una sola pieza. Además, no es necesario un disipador de calor.
En nuestro estudio, comparamos nuestros revestimientos con los métodos estándar de disipación de calor. Lo que demostramos es que se puede obtener un rendimiento térmico muy similar, o incluso mejor, con los revestimientos en comparación con los disipadores de calor. No obstante, un dispositivo que utilice la nueva solución es drásticamente más pequeño que uno que utilice disipadores de calor, que son voluminosos. Y esto se traduce en una potencia mucho mayor por unidad de volumen. Pudimos demostrar un aumento del 740% en la potencia por unidad de volumen.
Tarek Gebrael
Eso supone una gran diferencia en el mundo real.
Digamos que tienes varias placas de circuito impreso. Puedes apilar muchas más placas de circuito impreso en el mismo volumen cuando utilizas nuestro recubrimiento, en comparación con si utilizas disipadores de calor convencionales refrigerados por líquido o por aire.
Tarek Gebrael
Esta tecnología tiende un puente entre dos enfoques de gestión térmica distintos: la refrigeración a nivel de dispositivo cercano a la unión y la propagación del calor a nivel de placa.
Nenad Miljkovic, profesor asociado de ciencias mecánicas e ingeniería en la UIUC
Todavía están investigando la fiabilidad y la durabilidad de los revestimientos, que son fundamentales para su aceptación por parte de la industria. El trabajo ya ha demostrado que los revestimientos pueden utilizarse tanto en el aire como en el agua, lo cual es necesario para las aplicaciones de «refrigeración por inmersión».
El equipo está estudiando ahora la fiabilidad en agua hirviendo, fluidos dieléctricos en ebullición y entornos de alta tensión. También aplicarán los recubrimientos en módulos de potencia y tarjetas GPU a escala real, mientras que en el trabajo inicial sólo utilizaron simples placas de prueba.
Gracias a estos esfuerzos, la nueva solución debería dar un gran paso hacia la transición a la industria y la producción comercial para diversas aplicaciones, como la refrigeración de la electrónica de potencia, la gestión térmica de los centros de datos y la refrigeración de máquinas eléctricas.
Vía doi.org
Deja una respuesta